Engine Technology to Meet Emissions Regulations and Beyond
Advancements in engine systems will continue to focus on improving efficiency and reducing emissions.
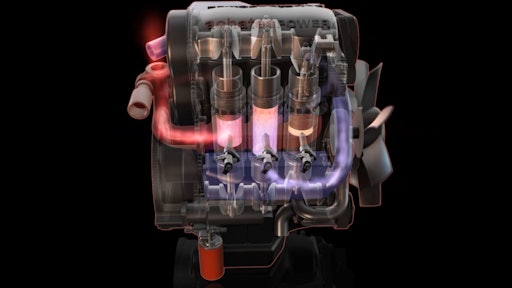
Although there is a lot of focus these days on alternative power systems such as batteries and fuel cells, internal combustion engines will continue to play an important role in heavy-duty applications. As such, it will be necessary for manufacturers to keep evolving their designs to optimize performance and reduce emissions.
“Almost every region of the world has air pollution regulations in place or is developing them,” says Gregory Pelton, Senior Manager – Sales and Application Engineering Construction, Industrial and Agriculture at MTU America Inc. “These ever more stringent emissions regulations require the deployment of new or optimized technology.”
MTU, like most engine manufacturers, has developed a platform of dual certified engineswhich meet EU Stage V and U.S. Tier 4 Final emissions regulations while also offering a solution for lesser regulated areas. Stage V is the most stringent regulation to date for the off-highway equipment industry; developing engines which meet it as well as other regional regulations eases installation and design costs for OEM customers by giving them the flexibility of using the same engine for various emissions regulations. MTU’s Series 1000, 1100, 1300 and 1500 engines are available with dual-certification for use in multiple global markets.MTU America Inc.
Developing these dual certified engines required optimization of the entire engine package, says Pelton. Continued optimization of the engine and aftertreatment system enabled reductions in fuel consumption as well as longer service intervals, providing customers with further benefits. These types of optimization efforts will also be necessary when new regulations are introduced to the industry, he says.
Nick Block, Director, Worldwide Marketing & Sales, John Deere Power Systems (JDPS), says leveraging the company’s experience to refine the technologies it has developed over the years aids engine optimization. Areas he says JDPS is focusing its efforts include improvements in package size, reducing overall engine weight, and integrating new generations of electronic control systems, which offer greater capabilities.
“In the future, we anticipate there will be a completely new generation of engine electronic control systems that will be more capable,” he says. “One trend we know will continue to evolve in the coming years is less reliance on physical sensors as engine control units continue to become more advanced and enable greater engine control and diagnostics performance.”
Block says JDPS used a next-generation engine control unit (ECU) in its 13.6L engine; the new ECU utilizes advanced model-based controls which enhance reliability and transient control.
John Deere’s 13.6L engine features a next-generation ECU utilizing advanced model-based controls which enhance reliability and transient control.John Deere Power Systems
Technology improves performance
Efficiency is a key area in which many manufacturers focus their design efforts. Block says JDPS this includes looking at ways to improve fuel efficiency. To do so, it is addressing combustion and air handling efficiency, as well as managing friction losses by leveraging advanced modeling techniques.
For its 13.6L engine, JDPS used a clean-sheet approach; designing the engine from the ground up better enabled the company to address many of the areas it wanted to improve. “One of the objectives of that project was to manage in-cylinder efficiencies,” he says. “We designed this engine for increased firing pressures to accommodate fast fuel burn while minimizing heat losses, leading to increased performance.”
“We recognize that if we’re going to make our transportation more sustainable, we need to make engines more efficient,” says Laurence Fromm, Executive Vice President of Business Development, Achates Power.
Achates Power is currently evaluating the use of opposed-piston engines. Though not a new concept, Fromm says it was previously thought that while opposed-piston technology was more efficient than conventional engines it would be a challenge to meet modern emissions standards. However, the company has found it to be the opposite; the technology he says is actually cleaner in addition to being more efficient.
He explains that in a conventional engine, there is a piston which goes back and forth in a cylinder. But in an opposed-piston engine, every cylinder has two pistons which come together. The piston crowns are what forms the combustion chamber. “There’s a lot of benefits to that architecture,” he says.
As there is no longer a cylinder head, efficiency can be improved because heat losses typically associated with cylinder heads are eliminated. Fromm says in conventional engines cylinder heads get very hot and aggressive cooling is needed, and all the heat is wasted energy. “We can take more of the energy in the fuel and turn it into useful work,” he says. Achates Power is developing an advanced combat engine for the U.S. Army which doubles the power pack density of other engines.Achates Power Inc.
Studies have shown an opposed-piston engine can be 13-15% more efficient due to the reduced heat loss and other benefits, he notes.
Achates currently has several major projects it is working on, one of which is developing an advanced combat engine for the U.S. Army. Fromm says power pack density—how much power can be put into a unit—is the main criteria for the Army. The entire engine system including the engine itself, fuel system and cooling system are part of this power pack because it all needs to be under armor.
Fromm says the engine it is developing with Cummins Inc. doubles the power pack density of other engines. “We have a smaller engine, a smaller cooling system, and because we’re more efficient we have a smaller fuel system,” he explains. “That allows us to deliver twice as much power per unit volume.”
This is important for a combat vehicle because it can move and accelerate faster and more easily climb hills, all of which makes it easier to engage and evade enemies.
By not having a cylinder head, heat losses are minimal; heat rejection is about 30% less than a conventional engine, says Fromm. This means the cooling system size can be reduced about 30% as well, which helps reduce space claim for the engine system. The engine itself is also smaller while providing more power density due to it being a two-stroke engine. “We get a power stroke in every cylinder on every revolution of the engine which is inherently more power dense than a conventional engine.”
Expanding fuel options
Libertine FPE is currently developing opposed free-piston engine technology which replaces the crankshafts with software control. Doing so would allow every combustion event to run optimally using real-time compression ratio control. This will enable engines to be even cleaner and more efficient, says Sam Cockerill, CEO of Libertine FPE.
It will also enable a fossil free future. In particular, it will allow the use of renewable fuels like ethanol and methanol. Making fuels which act like petrol and diesel is expensive and energy inefficient. “Making simple molecules like ethanol and methanol, it’s easy to do, it’s cost effective, it’s more energy efficient, and it has lower greenhouse gas impact,” says Cockerill.
However, to use these renewable fuels he says there is a greater need for more nuanced compression ratios which today’s engines are not able to do. Libertine is looking to address this issue by using software instead of a crankshaft which is essentially a thumping piece of metal that can not be controlled as well. “We’re putting the freedom to choose your compression ratio every cycle into the hands of combustion engineers, so they can make better engines for renewable fuels,” says Cockerill.
Enabling greater control over compression ratios provides more flexibility in the types of fuels engine manufacturers can use.Libertine FPE
He notes this is a challenge engineers have been trying to overcome for several years with various designs but generating electrical power whilst maintaining piston motion control has proved troublesome. Advances in power electronics, embedded controls and magnetic materials in recent years, though, has provided new opportunities.
Libertine is bringing together the electric components as well as control hardware and software into a platform which engine developers can then use to command compression ratio cycle by cycle, just as they do with fueling and ignition today. “By making that platform part of the technology environment that a combustion developer can use, it shortcuts the development of free piston engine products by years, possibly as much as a decade,” says Cockerill.
This means it could be possible to bring alternatively fueled engines to market faster, helping manufacturers and end use customers meet emissions reduction targets sooner. “If you replace the crankshaft with linear electrical machines, it’s a fuel flexible engine,” he says. While there are a few aspects that still need to be considered such as material compatibility in the fuel lines and injector choice, in general having control over the compression ratio enables fuel flexibility.
This in turn means that an engine can be designed to run on future fossil-free fuels such as ethanol and methanol whilst being backward compatible with fuels that are in use today. Cockerill says this flexibility solves the ‘chicken and egg’ problem that faces new engines designed exclusively for new fuels.
He says there is a lot of interest in Libertine’s technology for heavy-duty on- and off-highway engine applications. This is because battery-electric solutions alone will not be sufficient to meet emissions reduction goals due to the size, weight and power density needed, as well as lack of charging infrastructure in many cases. As such, internal combustion engines and the ability to use alternative fuels will be necessary in these applications. “Renewable fuels and internal combustion engines, those work today,” he says. “I think they will be a big part of the future.”
Many acknowledge that electrifying heavy-duty applications will be difficult, necessitating a mix of options to decarbonize the industry.
Meeting current and future emissions regulations
Reducing emissions will continue to be an area of focus for manufacturers as they and their customers look to minimize their environmental impact in the coming years. Governments around the world are also implementing stringent carbon reduction goals which will necessitate OEMs and engine manufacturers finding ways to reduce emissions further.
The latest emissions regulations have mainly been focused on the heavy-duty on-highway market, such as the Phase 2 Greenhouse Gas (GHG) standard for medium- and heavy-duty vehicles through model year 2027 in the U.S. However, many in the industry anticipate similar regulations from the on-road side will make it into the off-highway market at some point in the future as well.
“The on-highway emissions regulations have typically paved the way for subsequent off-road standards,” says Pelton. “The Phase 2 GHG standards are a great example of what most in the industry expect to see in off-road equipment as well. It will become whole vehicle optimization with the diesel engine itself playing only a part in the total solution. This will require even stronger partnerships with our OEM customers as we will have to work together even more closely to produce products demanded by both the users and whatever regulations are in place.”
Fromm says one of the big advantages of Achates’ opposed-piston engine design is its ability to reduce NOx (oxides of nitrogen) emissions which will be beneficial for both on- and off-highway equipment manufacturers. “California just passed NOx emissions for on-road vehicles requiring another 90% reduction in NOx starting in 2027,” he notes. “They said they’re going to now focus on off-road as their next area to take a look at to lower NOx.”
Achates Power’s 10.6L heavy-duty diesel engine in a Peterbilt 579 truck which will be driven in fleet service in California later in 2021.Achates Power Inc.
To reduce NOx, he says it is necessary to quickly get the selective catalyst reduction (SCR) system as hot as possible to ensure only harmless nitrogen and oxygen come out of the vehicle’s tailpipe. An opposed-piston engine is able to achieve this as it has very high enthalpy to heat up the catalyst while achieving low engine out NOx. “The reason we can do this is because in the opposed-piston engine, we have intake ports on one side of the engine and exhaust ports on the other side. It’s the piston motion that opens and closes the ports. And that port timing allows us to scavenge the cylinder in one direction. So the exhaust ports open first, the exhaust goes out, the intake ports open, we put new fresh air in, the ports close and we compress and ignite,” explains Fromm.
“We’re able to dynamically change how much exhaust gas we leave in the cylinder,” he continues. “When we want to generate a lot of enthalpy, we go into what we call a catalyst light off mode where we reduce the flow through the engine.”
READ MORE: Achates Power Receives DOE Award to Develop Medium-Duty Opposed-Piston Engine
Maximizing the amount of exhaust gas that stays in the cylinder enables it to get hotter as it sits in the cylinder; the hotter it is, the better able it is to quickly light the catalyst. Fromm says because this exhaust gas has already been combusted, it has the effect of internal exhaust gas recirculation (EGR) which is commonly used for reducing NOx. Whereas a conventional engine will have to pump exhaust gas in and out, the opposed-piston engine is able to reduce this extra work through its dynamic control of the gas and leave it in the cylinder. “We have engines on our dynamometer now that we’ve measured the ability to meet the 2027 California requirement for a 90% reduction using conventional aftertreatment systems available today,” he says.
“Conventional engines have been improved a lot over the last 30 or 40 years,” says Fromm. “But every time we try to make them less harmful in terms of CO2 or criteria emissions, it’s getting harder because we’ve already wrung so much out of it. We’ve reached the point of diminishing returns; it’s getting more expensive to make it better.”
With the opposed-piston engine though, he says there is still room to continue making improvements. “The opposed-piston engine has built-in advantages that allow us to go beyond what’s going to be required in 2027 to reduce both CO2 and NOx even more.”
Block also agrees that additional NOx reduction standards being considered for on-highway vehicles will eventually make their way into off-highway emissions regulations. “This will impact the industry as manufacturers continue to keep track of nuanced regulations from country to country while helping their customers manage necessary transitions,” he says.
The Integrated Emissions Control System (IECS) incorporates the components right into the system rather than utilizing a separate mixing pipe, enabling it to be more streamlined and compact.John Deere Power Systems
To meet these and any other new emissions regulations, Block says it will be important to focus engineering efforts on combustion technology. “We need to continue to consider engine design elements such as power cylinder, cylinder heads, air systems, and fuel injection parameters. It’s not one single thing, but rather a variety of refinements for system optimization.”
Managing air flow through the engine will be important, as well, especially if the on-highway NOx reduction standards go into effect for off-highway applications, he says. Improving the efficiency of aftertreatment systems will also be important.
The company’s Integrated Emissions Control System (IECS) is an example of the improvements that can be made to an aftertreatment system. Block says it incorporates the components right into the system rather than utilizing a separate mixing pipe. Improvements in the catalyst and substrate technologies allow for smaller sizes while also reducing the amount of metal previously used. “These combined improvements allow for an improved, streamlined aftertreatment design that is more compact, flexible and lower in cost.”
Virtual analysis will play a key role in continued development efforts. Block says it allows the company to define and optimize engine subsystems to achieve performance enhancements before creating any hardware or building the combustion system. “We’re continuing to explore new technologies that enable advanced combustion concepts for continued improvement of the diesel engine,” he concludes.